Enhancing Operational Efficiency in Manufacturing: Rineer Revival
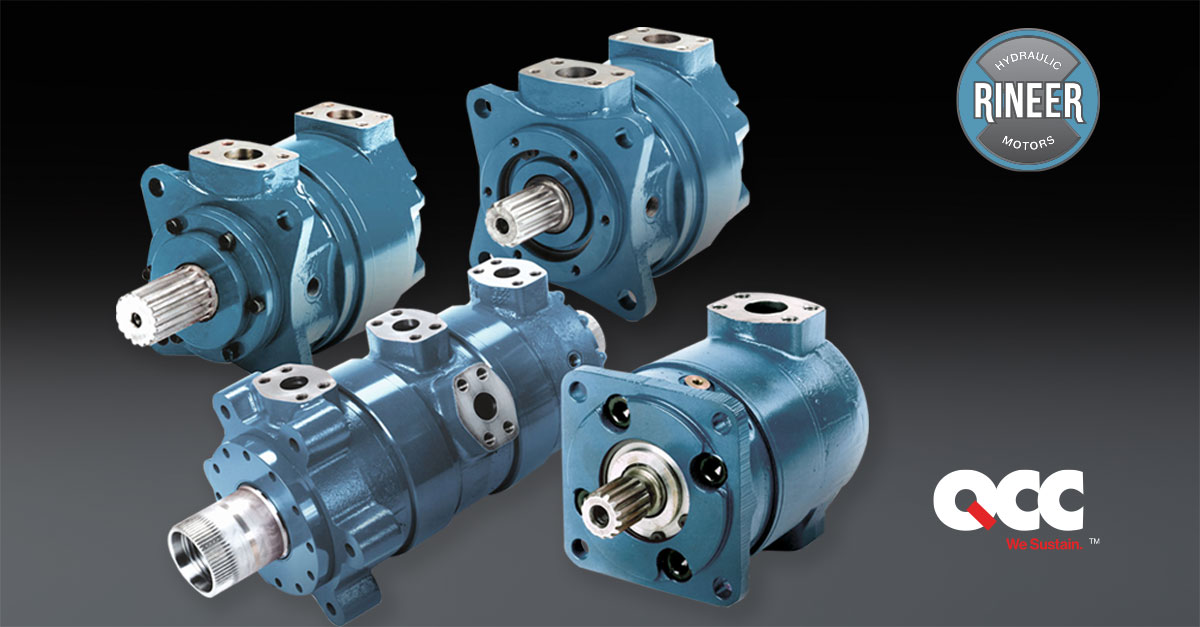
Testimonial
“We partnered with the team at QCC to revitalize the Rineer product line, and the results have been nothing short of transformative. Through their expertise, we achieved a 92% recovery in our backlog, while reducing lead times by 75%. Through continuous improvement efforts, QCC was also able to improve suppliers’ performance, with 50% enhancements in both throughput and on-time delivery.
Thanks to the new strategies implemented, we are now consistently able to achieve a 90% on-time delivery rate. The ability to flex the workforce has allowed us to adapt swiftly to changing production needs without sacrificing quality or efficiency. Additionally, improvements have been made to the warranty review process, which has been streamlined to reduce containment times drastically.
This partnership has not only enhanced our operational efficiency but has also boosted our customer satisfaction levels. We are now better positioned to meet customer demands and achieve our business goals. I recommend the QCC team to any manufacturing organization looking to drive significant improvements for their product line.”
Karl Lindblom, Senior Vice President Hägglunds
Large Hydraulic Drives Business Unit, Bosch Rexroth
Executive Summary
The Rineer motor product line is known for its patented “vane-crossing-vane” design allows for both low speed/high torque and high speed/high torque operation, resulting in an optimum power-to-weight ratio, smooth output over a wide speed range, and the unique capability to deliver maximum torque at zero rpm. Despite the products’ superior performance, the product line had faced operational challenges in recent years following its move from San Antonio, TX, to Fountain Inn, SC.
Through focus and attention, QCC was able to make significant operational improvements to the Rineer manufacturing line, resulting in a 92% improvement in on-time delivery, a 75% reduction in lead time, and a 50% enhancement in supplier throughput and on-time delivery. By implementing targeted strategies, the manufacturing line successfully reached a 90% on-time delivery rate, positively impacting customer satisfaction and overall business performance.
Introduction
In today’s competitive manufacturing environment, timely delivery and efficient processes are crucial for success. This case study focuses on a manufacturing line that faced challenges with delivery delays and inefficiencies. The objective was to enhance operational performance through strategic improvements in production and supply chain management.
Methodology
The approach involved a comprehensive assessment of current processes, identifying bottlenecks and areas for improvement. Key methods included:
- Process Mapping: Analyzing workflow to pinpoint inefficiencies.
- Supplier Engagement: Collaborating with suppliers to improve their throughput and delivery performance.
- Lean Manufacturing Principles: Implementing lean techniques to streamline operations and reduce waste.
- Data Analysis: Reviewing historical delivery data to identify patterns and delays.
Results
1. On-Time Delivery Improvement:
- Pre-improvement on-time delivery was at 50%. After the transfer to QCC, this improved to 90%.
2. Lead Time Reduction:
- Pre-transfer lead times were 12 to 14 months. After the transfer, lead times were reduced by 75%. Lead times are now at 16 weeks, with the aim of further reducing them to 12 weeks sometime in Q1 2025. Improved lead times allow for faster turnaround times on orders, reduced inventory demand for customers and end-users, and improve timely support for critical prototype orders.
3. Supplier Throughput:
- Supplier throughput and on-time delivery increased by 50%, enhancing the overall supply chain reliability, and providing dependable lead times for future shipments.
Analysis
The analysis revealed that bottlenecks primarily occurred in the supplier coordination and operational implementation stages. By adopting lean manufacturing practices and improving communication with suppliers, the manufacturing team could streamline its operations. The reduction in lead time was critical in meeting customer demands more swiftly, while the improvements in supplier performance ensured a more reliable supply chain.
Recovery Methodologies and On-going Initiatives
- Continuous Improvement: Establish ongoing assessment processes to ensure sustained improvements.
- Supplier Development Programs: Invest in training and development for suppliers to further enhance their capabilities.
- Workforce Development: Cross-training enhances the skill set of the workforce, allowing employees to contribute to different areas of production. This can lead to more efficient operations and reduced reliance on specialized roles. Employees who are trained in multiple roles can easily shift between tasks as needed, helping to maintain production flow during peak times or when unexpected absences occur. Of course, it goes without saying that a happy and engaged workforce will provide results through improved retention.
Conclusion
The improvements that were implemented resulted in substantial operational efficiencies. The increased on-time delivery rate and reduced lead times not only enhanced customer satisfaction but also positioned the company more favorably in the competitive off-highway market.
Want to schedule a meeting via email?