Things To Consider When Deciding To Extend Service Life Of Equipment Or Buy New
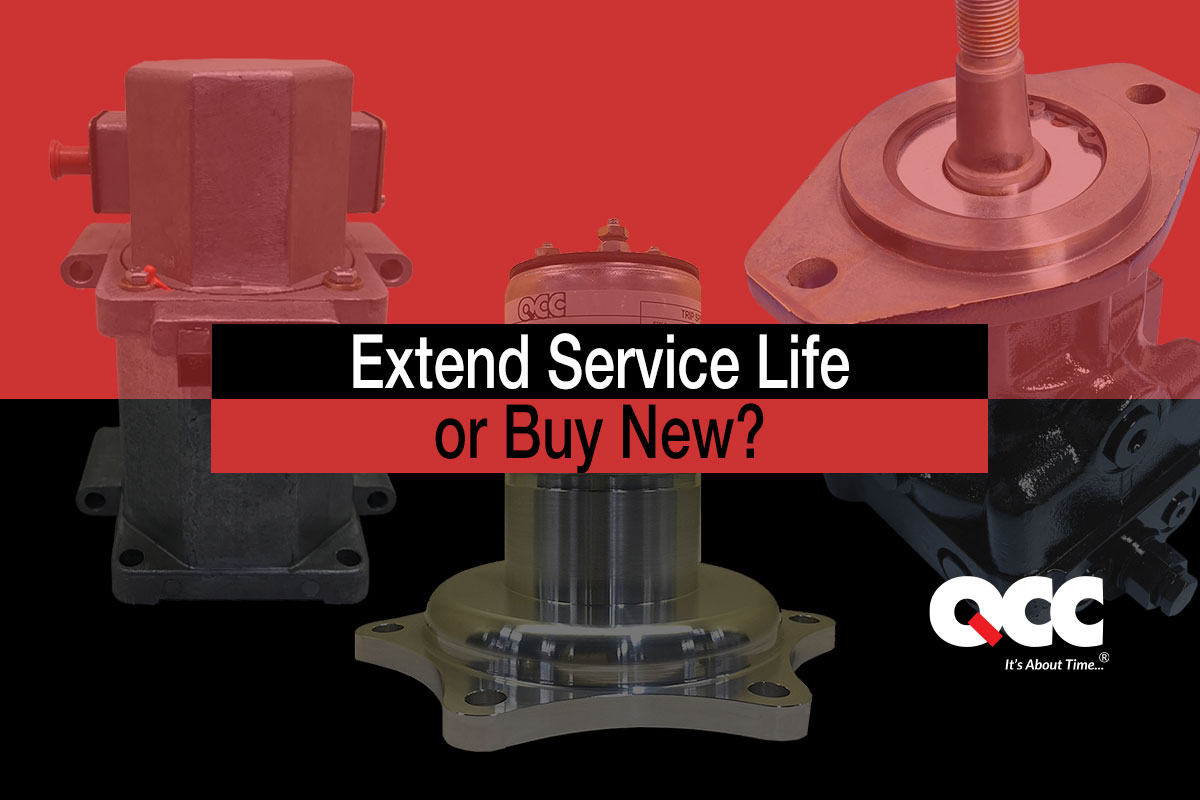
Considering the total cost of ownership (TCO) is an important aspect when deciding whether to invest in service parts or purchase a new machine. TCO takes into account the total cost of a product or service over its entire lifecycle, including its purchase price, installation costs, maintenance and repair costs, operating costs, and disposal costs.
One primary consideration is that the cost of service parts can vary significantly from production run parts, depending on factors such as the complexity of the part, the volume of production, and the lifecycle phase of the equipment. In general, service parts tend to be more expensive than production run parts, as they are often produced in smaller quantities and may require additional processing or customization to meet specific customer needs.
In addition to the production costs, service part costs may also include additional costs such as inventory, shipping, handling, and storage, which can further increase the overall cost. However, the cost of service parts may be offset by the benefits they provide in terms of customer satisfaction, reduced downtime, and increased equipment reliability.
Another consideration is who to source your service parts from. There are a variety of service part offerings available on the market, including dealer networks, OEMs, licensers, and less reputable sources like eBay. Making the correct decision on who to source the parts from is almost as important as the decision to maintain or replace equipment.
It is important to consider the total cost of ownership when comparing the cost of service parts to purchasing a new piece of equipment. Taking into account factors such as maintenance costs, repair costs, and the cost of downtime, it is often more cost effective to extend the life of a piece of machinery than it is to replace it. In some cases, investing in high-quality service parts may be more cost-effective in the long run, as it can help to reduce overall maintenance and repair costs and can extend the service life of the equipment.
Here are the steps to consider when evaluating TCO for service parts:
- Identify the costs: Begin by identifying all the costs associated with the service parts over their entire lifecycle, including purchase, installation, maintenance, repair, downtime, and disposal costs. Be sure to include all relevant costs, such as labor costs, shipping costs, and inventory carrying costs.
- Estimate the expected lifespan of the equipment: Determine the desired lifespan of the equipment, considering factors such as wear and tear, environmental conditions, and usage patterns. This will help you to estimate the number of times the part will need to be replaced over its lifespan.
- Calculate the TCO: Calculate the total cost of ownership by adding up all the costs associated with service parts, as well as maintenance and repair downtime. Weigh these costs against the hourly value of the equipment when it is in service. This will help you understand the true cost vs benefit of service or replacement over the equipment’s expected lifespan and help you to make a more informed decision when evaluating different service parts options.
- Consider reputable sources: It's important to consider not only the costs but also the benefits of investing in the right service parts. For example, high-quality parts from reputable dealers may last longer, require less maintenance, and reduce downtime, which can result in significant cost savings over the long term.
By considering the total cost of ownership, you can make more informed decisions when evaluating whether to extend the service life of your equipment and ensure that you are selecting the most cost-effective solution for your company.
Want to learn more about QCC Legacy After Market Parts programs?